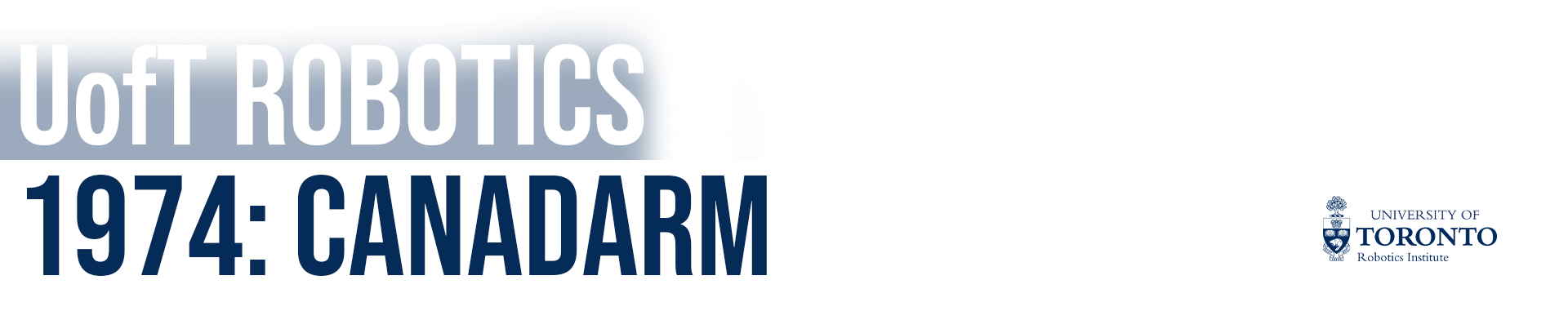
Scientists told NASA that the Shuttle Remote Manipulator System — the proposed robot arm that would capture and manoeuvre payloads on the Space Shuttle — would require six degrees of freedom to do its job. Then they told NASA that it was not possible to achieve six degrees of freedom in a flexible, light-weight arm that was orbiting the earth and not fixed to the ground.
Canada disagreed. Learn how the University of Toronto helped to make the impossible possible by bringing six degrees of freedom to a moving target!
By Joan DaCosta. With contributions from: Peter Hughes and Andrew Goldenberg (University of Toronto Professors Emeriti), Gabriele D’Eleuterio and Chris Damaren (Professors at the University of Toronto Institute for Aerospace Studies - UTIAS), Drs Ravi Ravindran and Phung Nguyen (UTIAS Alumni and SPAR Scientists who worked on Canadarm & Canadarm2), Dr Cameron Ower (UofT alumnus and Chief Technology Officer for MDA -- formerly SPAR), and Lydia Dotto (author of A Heritage of Excellence: 25 Years at Spar Aerospace).
Canada is a large land mass with a small population, which from the 1960s forward has been approximately 10% of the population of our neighbour the USA. We have long been used to living in the shadow of this giant, so when it came to the multibillion-dollar US space program, it seemed that Canada could only watch from the sidelines.
In fact, when NASA first issued the call for “a tool to function flawlessly in space with the dexterity of a human arm” for their new Space Shuttle program, the Canadian Space Agency (CSA) didn’t even exist. But this big little country answered NASA’s call, and thus began a long and rich history of Canadian excellence in robotics – and it is no surprise that the University of Toronto was there from the beginning.
Why Canada?
Because they wanted international involvement, in 1969 NASA invited Canada to participate in their space shuttle program. However, they weren’t sure what Canada would do exactly. At first, NASA was considering an elevator-type mast for deploying satellites, but then they became aware of a fuel injection robot that had been developed by Canadian company DSMA-Atcon for the CANDU nuclear reactor. It was this Canadian fuel injection robot that stimulated the idea for what would become the Canadarm.
In 1974, NASA awarded Canada the contract to design the Shuttle Remote Manipulator System (SRMS) and associated simulator facility (SIMFAC). Because there was no Canadian Space Agency at this time, it was the National Research Council of Canada that coordinated the industry team that was led by SPAR Aerospace (now MDA), and included DMSA-Atcon, CAE and RCA as subcontractors.
Making the “impossible” possible
Photo credit: NASA/Winston Scott (1996)
University of Toronto Professor Emeritus Andrew Goldenberg, a pioneer in robotics who worked for SPAR from 1975-81, cannot help but get excited when he talks about working on the design of the Canadarm: “Together we created something amazing that was way ahead of its time, something that had never been done before, that was unique in every sense.”
The SPAR group that worked on Canadarm’s initial design included roughly a dozen highly capable people, including Professor Peter Hughes from the University of Toronto Institute for Aerospace Studies (UTIAS), and two of his PhD graduates, Dr. Rangaswamy (Ravi) Ravindran and Dr. Phung Nguyen, both of whom worked for SPAR on Canadarm and Canadarm2 (C2). According to Goldenberg, Hughes was the Canadarm’s “master of development”, and his mathematical models were critical to the project’s ultimate success.
One of the requirements for Canadarm was that it had to be very light in mass in order to add as little weight as possible to the launch mass. It also had to be small in volume to fit into the shuttle. However a consequence of having to create such a light arm was that it would bend and twist. And therein lay the problem: achieving 6 Degrees of Freedom (6-DoF) for a flexible arm moving through space had never been done before!
The traditional method of calculating 6-DoF is to use the centre of mass as the reference frame, which is the point against which all other positions are measured. However, that method only works for stationary and rigid arms, like the industrial arms found in factories. This is why, when the US scientists tried to calculate the dynamics for the arm using the mass centre, they failed.
Prof. Peter Hughes' "aha!" moment came when he understood that he was dealing with a rotational system of dynamics: that the arm would bend and twist along its entire length. Moreover, each joint in the arm would have 3 Degrees of Freedom (3-DoF).
This meant that the entire system contained a myriad of variables that made it extremely complex to analyse.
Now, armed with a clearer view of the problem, Hughes understood that if he used the shuttle attach point as the primary origin for analysis—not the system mass center—this would simplify the analysis. The mass center would, of course, continue to orbit the Earth.
Using this method, Hughes succeeded where others had failed. He ultimately developed a completely new approach to the dynamics of robotic arms using elastic links, where “each joint had six degrees of freedom and the arm had six links so that it could grab anything from any angle and move it anywhere."
The algebraic language of Hughes' math model was so complex that the notation was considered a contribution in and of itself. Moreover, his dynamics analysis was used to design both the Canadarm and the associated simulators upon which all the initial astronauts were trained.
Hughes received the prestigious John H. Champman Award of Excellence for his revolutionary work. When presenting the award, the Canadian Space Agency (CSA) President stated that “...Canada could not have built Canadarm for the NASA space shuttle were it not for Dr. Hughes’ complete analysis of Canadarm’s dynamics and control."
Why is arm flexibility such a big deal?
According to NASA, the 50-meter long Canadarm was "accurate enough to put a peg in a hole given 60/1000 of an inch of clearance." Dexterity and flexibility are a must when performing precision operations such as this.
But it is much more difficult to control a flexible arm than a rigid arm, particularly in peg-in-hole tasks where the system must account for interacting objects, as well as arm vibration frequencies that vary with its motion and must be accurately represented in simulations.
The booms in the Canadarm's upper and lower arms are fairly rigid, so the system gets its flexibility primarily from its joint gearboxes. The Canadarm was designed to meet its stiffness budget, which is 1662 N/m at the tip of the arm when the arm is fully extended. It is difficult to visualize the flexible motion of the arm via direct viewing.
With contributions from Drs Phung Nguyen and Ravi Ravindran.
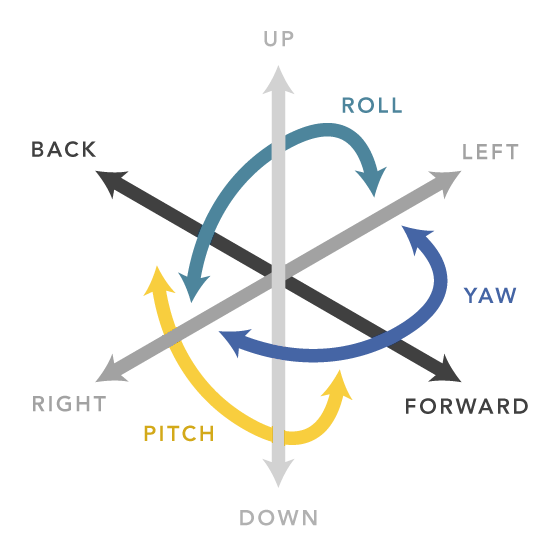
Six Degrees of Freedom (6-DoF)
All Singing, All Dancing
While Hughes worked on Canadarm’s dynamics, Goldenberg was second in command of the control system group, which analyzed the concept, approaches, and methodology before the system’s detailed design was completed. Meanwhile, Hughes taught a course on the dynamics of space systems to SPAR’s entire Canadarm team, which helped the two groups develop a common language for communication and enabled them to work closely together.
Hughes’ analyses were used not only for the Canadarm, but also for the simulation facility, SIMFAC, that would be used for testing the Canadarm. Goldenberg also worked on the simulation with a large dynamics and control group, to which Hughes’ team contributed critical math models.
In the end they developed two simulation models to test the Canadarm. One model was called “RIGID,” and the other was called “ASAD,” which stands for “all singing, all dancing.” “RIGID” was for testing every part of the arm except for its flexible properties. Hughes’s math models were added to the “Rigid” model to achieve the complexity of “ASAD”, which Goldenberg describes as being a "variety of movements – the links moved and danced ... they had to be elastic for the arm to operate correctly.”
Canadarm design and computer simulations
The engineers at SPAR turned to the human arm for ideas, which led to the design of the anthropomorphic Canadarm. Canadarm has 6 joints: 2 at the “shoulder”, 1 at the “elbow”, 3 at the ‘wrist”, which is the minimum possible configuration for a 6-DoF arm. In order to support their arm design, SPAR first developed a dynamics simulator named “RIGID”, which was based on the formulation of rigid multi-body dynamics available in 1975. In RIGID, the arm structural flexibility is ignored, while retaining the flexibility of the six joint gearboxes.
It was well known that structures and control interaction can lead to failure if the control system is not designed properly. Consequently, the dynamics simulator needed to be upgraded to include the arm structural flexibility in its dynamics model. SPAR contracted Professor Peter Hughes from the University of Toronto Institute for Aerospace Studies (UTIAS) to develop a new formulation for the dynamics of flexible multi-body system where the bodies are connected to one another in a chain-like fashion. The model that Hughes created was then implemented in a different simulator named “ASAD” (a term coined by SPAR engineer Cam Trudel and which stood for All Singing All Dancing), while retaining all other models in RIGID.
When the “flexible” components of the arm were turned off, ASAD produced the same results as RIGID, although they were based on different formulations and different implementations. Indirectly, they were validated against each other!
The same model created by Hughes was implemented in a real-time simulator called “SIMFAC” (for SIMulation FACility), which could simulate in real-time the unloaded arm and the arm loaded with a 32,000 lb payload. SIMFAC was used to support Canadarm’s control software design and to train NASA astronauts until NASA could develop their own simulator.
With contributions from Drs Phung Nguyen and Ravi Ravindran.
There are no tow trucks in space
According to Hughes, you can’t put a complicated piece of equipment in space without first testing it, because you can’t fix it if something goes wrong. In other words, there are no tow trucks in space.
The Canadarm was designed using a fail-safe philosophy, meaning that if it failed in space it would cause no harm to the Shuttle and/or the astronauts. In the event of a failure, its control system would allow the astronauts to tow it safely back to its stow position to await the Shuttle landing. Remarkably, this scenario never occurred in the life of Canadarm.
Possible failures in the Canadarm were simulated extensively in ASAD and SIMFAC. Simulations were also carried out to determine the envelope of arm operation in case the arm characteristics were not “as designed”, but still within their min and max limits. Such a system demands accuracy and attention to detail, which is why the simulation models were critical.
The equations that predicted how the manipulator system would behave included variables of joint angles, deflection of links, as well as forces and torques. According to Professor Gabriele D’Eleuterio (UTIAS), who did his PhD with Professor Peter Hughes and worked on Canadarm2: ”You start with Newton’s laws, plug in the variables you know and then crank out the ones you want,” but this was a lengthy and complicated process made more difficult because the work was being done in the early computer era.
Professor Chris Damaren, Director, UTIAS, an expert in spacecraft dynamics and control who helped to validate simulation codes for C2 during his PhD work, explains that “the dynamics analysis of flexible multi-body systems performed by Professor Peter Hughes and colleagues were essential to the design and operation of Canada’s space robotics systems. The simulation programs based on their algorithms were a great success and were used for ongoing operations until the original Canadarm was decommissioned in 2011.”
According to the archives, SPAR built the Canadarm's SIMFAC wireframe simulator based on the models developed by Hughes' group, and NASA astronauts came to Toronto to be trained on SIMFAC until the early 1980s. The astronauts who subsequently worked with the Canadarm confirmed that the simulator was indeed very accurate.
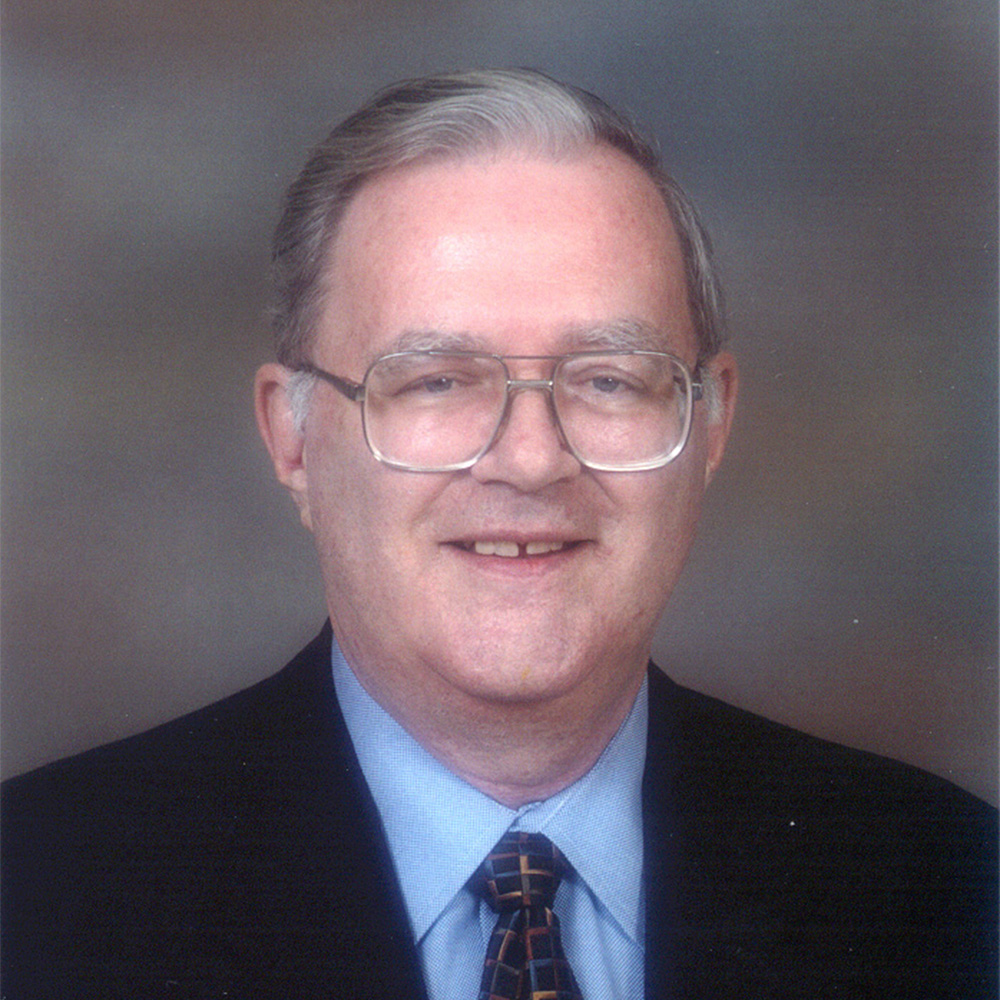
Dr. Peter Hughes, Canadarm Dynamics Lead (Professor Emeritus, UTIAS)
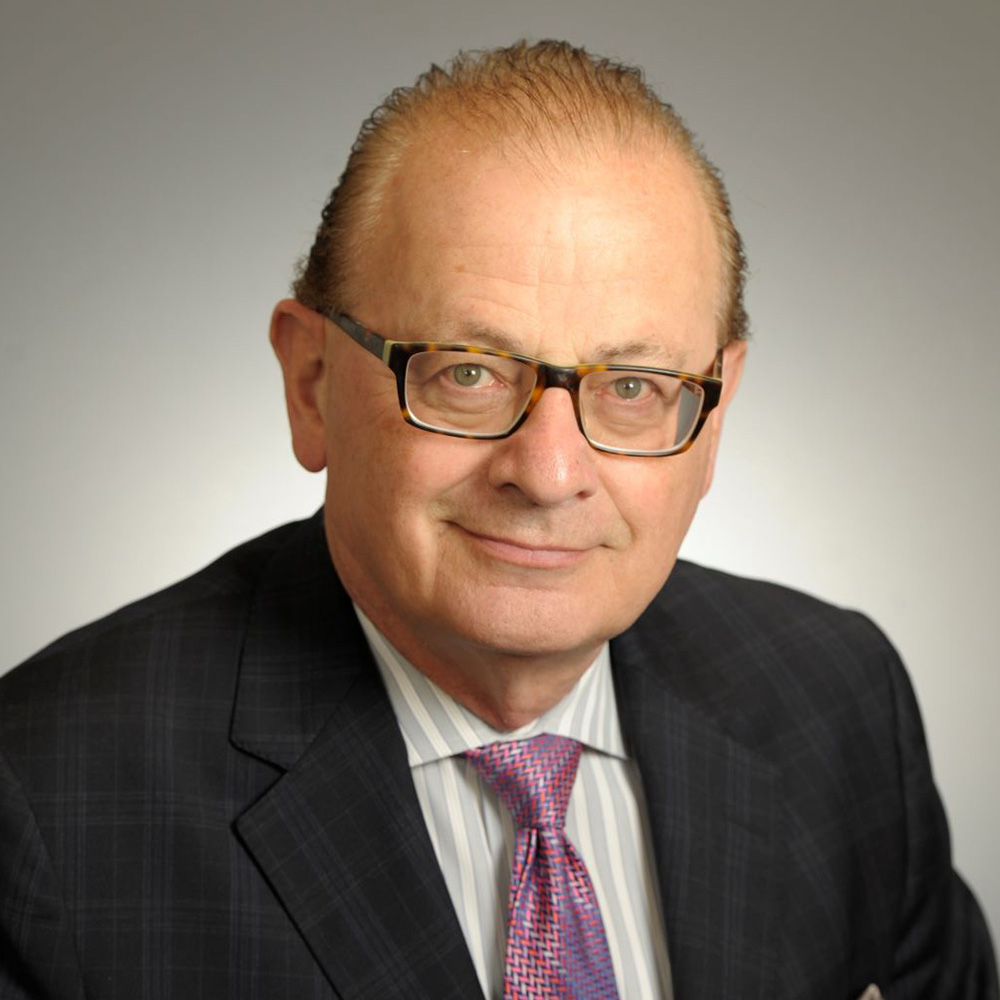
Dr. Andrew Goldenberg, Canadarm Controls Group (Professor Emeritus, MIE)
Find out why the team had to hail a cab every day
According to SPAR archives, the early simulation models were run on computers that ran on punched cards. There were a few thousand lines of code in the simulation, and at the beginning of the Canadarm project, every day the scientists would put in more conditions, send the box of punched cards off by taxi to a central computing centre in Toronto and then wait to get the results the next day.
Eventually SPAR got a card reader, which was linked to a mainframe computer to execute ASAD, so it was no longer necessary to hail a cab.
With contributions from Drs. Cameron Ower and the SPAR archives, Ravi Ravindran and Phung Nguyen.
Computer simulations, air bearing testing and on-orbit testing
The Canadarm was first tested on orbit in November 1981 without any payload. In subsequent tests, the arm was loaded with payloads of increasing mass, including the PFTA (Payload Flight Test Article) which was built to simulate a 32,000 lb payload. Flight data was analyzed to verify the arm performance in an effort to commission it for use in space.
Flight data was also compared with ASAD simulation results as part of ASAD validation. Eventually, ASAD was declared as having truthful representation of the Canadarm by NASA; it was then used later as a benchmark for the validation of other Canadarm simulators in the USA. The role of simulation in the development of the Canadarm was proven to be essential and was adopted in the development of its successor, Canadarm2.
With contributions from Drs Phung Nguyen and Ravi Ravindran.
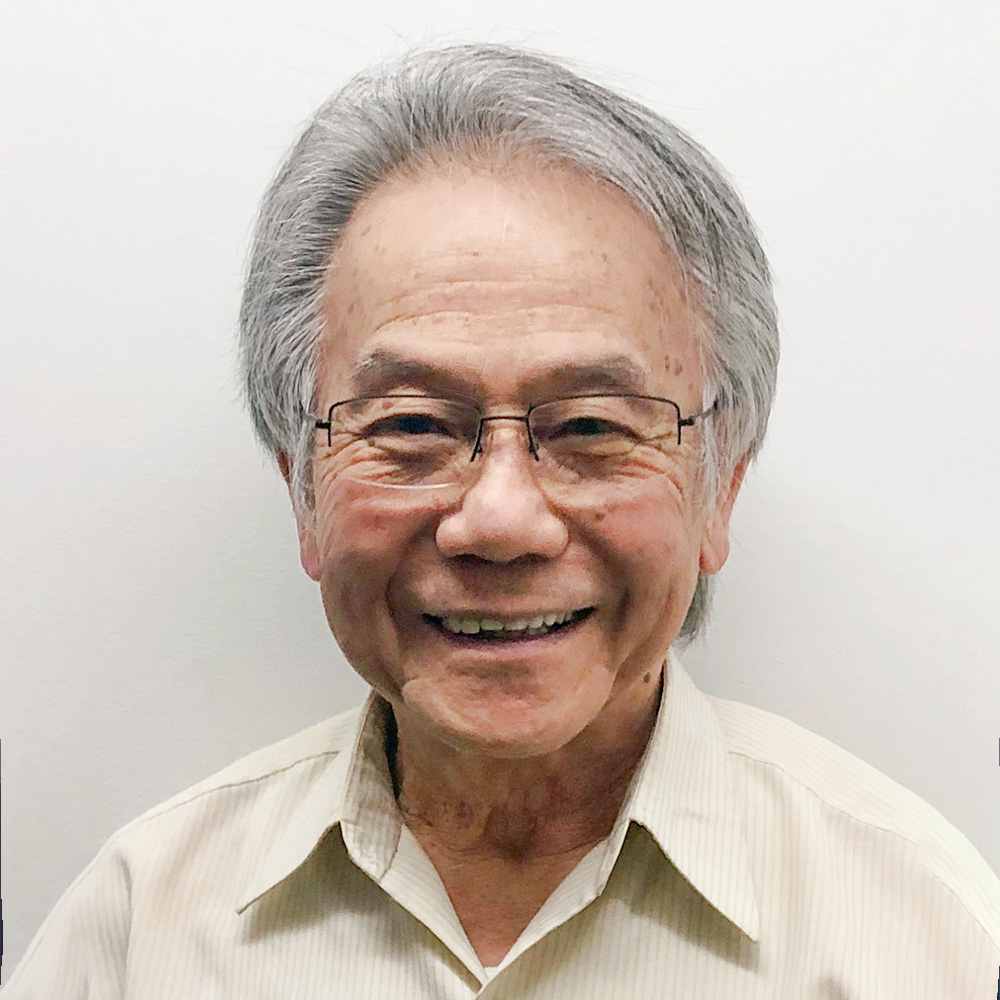
Dr. Phung Nguyen (UTIAS alumnus)
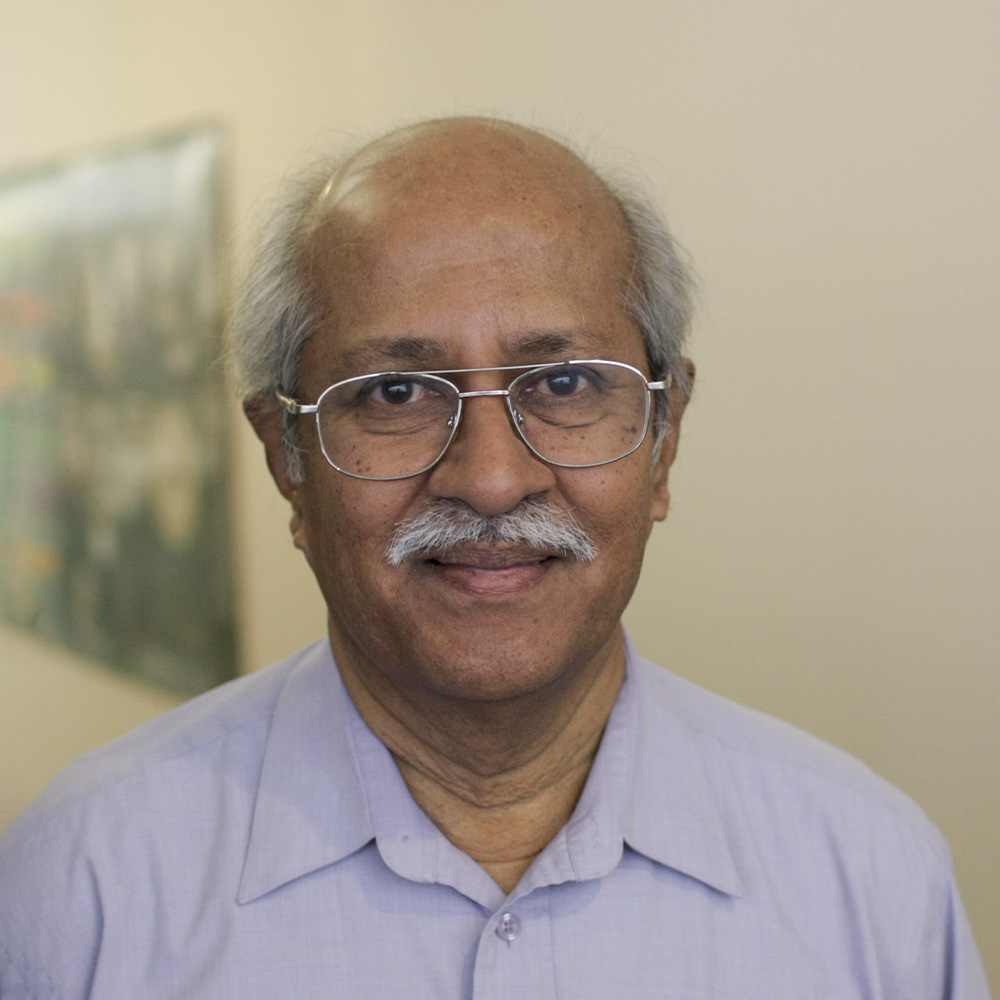
Dr. Rangaswamy (Ravi) Ravindran (UTIAS alumnus)
First exposure to real robotics
It took five years to develop and complete the Canadarm and SIMFAC. Throughout the process there were rigorous formal design reviews that, according to Goldenberg, were run “like military development programs” with NASA representatives regularly travelling to Toronto to meet with the scientists.
The arm had to be constructed of very light materials and, in the end, was so light that it could not support itself under the weight of earth's gravity and had to be held in a flat floor on air bearings when in the lab.
In February 1981, the $100 million, 50 metre long, 400 kg Canadarm, that in space could move around 29,500 kg objects, made the trip via truck from Toronto to the Kennedy Space Center where it was presented to NASA as Canada’s contribution to the Space Shuttle Program. It was then scheduled for testing in space on the 2nd shuttle flight, which launched in November 1981.
Photo credit: NASA (2008)
Photo credit: Canadian Space Agency (2005) - image enhanced. Canadarm, circa 1970s, shown without its white thermal protective sleeve in the clean room at Spar Aerospace in preparation for ground testing. So light weight that it could not support itself, the Canadarm hovers above an air-bearing -- the silver-grey structure that runs underneath its length. By creating a thin gas film between itself and the arm, the air-bearing acts as a lubricant that protected the arm from being damaged by its own weight during movement.
Due to a shuttle malfunction, the November mission was shortened and the Canadarm testing was to be rescheduled for the next shuttle flight. However, mission commander Joe Engle and pilot Dick Truly had other ideas. They pulled an all-nighter in space that allowed them to accomplish 90 to 95 percent of the objectives of the mission, which they said “was so much worth it.”
Engle describes his first experience of operating the Canadarm as being "like an extension of your own arm, I was just enamored with how neat it was, how much like the human arm it was. How intuitive it was to use the arm. It was my first exposure to real robotics.”
Henry Kaupp, a deputy branch chief in NASA’s Automation, Robotics and Simulation Division concurs with Engle: “This was the first space robotics of any size. It was a brand new design. No one had ever done this before.”
To say that the Canadarm was a success is an understatement.
In the 2006 NASA celebration of the 25th anniversary of Canadarm, Robert Ambrose, a branch chief in the Automation, Robotics and Simulation Division at NASA's Johnson Space Center said: “The kinds of things we’ve seen Canadarm do are just the beginning … All the advances we’ve seen in mobile robots are going to be seen in manipulation robots in the next 20 to 30 years. And the remote manipulator system [Canadarm] will be remembered as one of the pioneers.”
Canada paid for the development and the building of the first Canadarm and after the tremendous success of the first arm, NASA purchased four more.
Want to know just how successful the Canadarm was? Read NASA’s entire 25th anniversary review.